As of 2025, our slate of available services at Kingfisher Labels includes a wide range of flexographic printing options and customisations. Flexography is the modern answer to the historic letterpress, and flexo methods will only continue to improve with time, investment and innovation.
You’ve undeniably come across flexographic labels in your life—even if you didn’t pay much attention to their existence. They’re used on all manner of products and can be formed of various materials, running the gamut from sweet wrappers to beer bottle labels.
But, if you’re curious about how flexo actually works (and how it could benefit your business), you’re in the right place…
What is flexographic printing?
Flexographic printing is an increasingly popular way of producing bespoke labels quickly and efficiently. Flexo is fast, adjustable, and well-suited to printing large areas of solid colour, and there’s not much that couldn’t be printed flexographically in 2025.
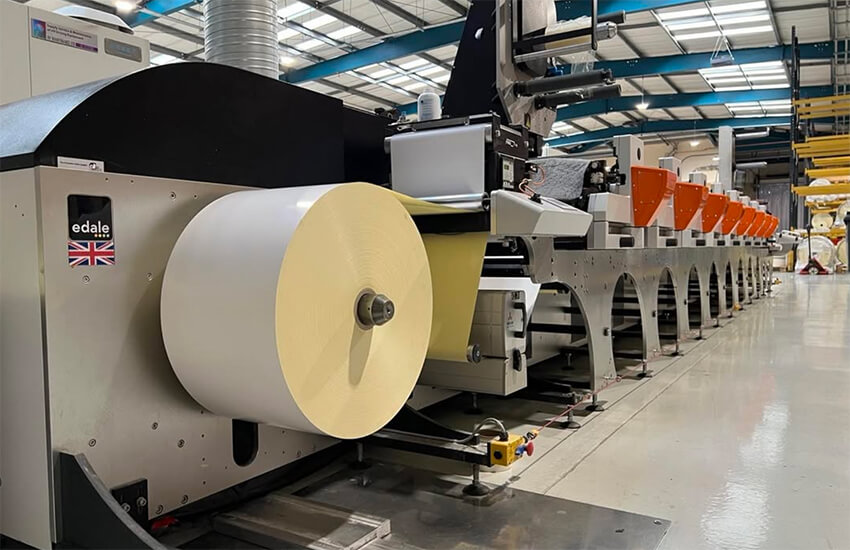
Why choose flexo?
There are six key benefits to self-adhesive labels produced using the principles and technologies of flexography:
- Substrate flexibility: Flexo works on numerous materials, from metal films to paper and plastic. This diversity also encompasses non-porous substrates, which is one of the reasons you’ll often see flexo deployed for packaging in the food and beverage industry.
- Colour and foil options: At Kingfisher, we offer our customers flexographic printing options in up to 10 colours. We can also provide gloss, matt and textured varnishes—and accommodate the addition of embossing or foil stamping to create metallic accents.
- Design versatility: We can use flexo for pressure-sensitive labels, multi-layer labels, double-sided labels, shrink sleeve labels, flexible packets, etc. Whatever the product you have in mind, the odds are high that there will be an appropriate, well-suited flexographic option.
- Reusability and easy maintenance: Once a plate is produced for flexographic printing, this plate is reusable, increasing cost efficiency and ROI in accordance with the length of a print run. Flexo presses are also easy to maintain, lengthening production lifespan and overall ROI.
- Efficiency and value: The flexographic printing process is expedited compared to digital label printing because substrates are web-fed from large rolls rather than individual sheets. This winds up especially cost-effective for large print runs with tight turnaround times.
- Quality and durability: Thanks to numerous innovations in the field, flexo methods in 2025 can achieve an incredibly high-quality finish for your labelling products. This includes durability, as flexo labels can be reinforced to add resistance to everything from water to UV.
Opt for innovation and elevation
Flexo methods are some of the best, most versatile forms of label printing technology available to us in today’s packaging industry. There’s a reason these highly customisable and versatile labels are everywhere—in fact, there are several, as we’ve established.
If you’re interested in exploring your flexographic options, get in touch for an obligation-free conversation with Kingfisher Labels.